So I decided to build one. Not going to start from scratch though. At my friends surplus store two Hamilton Starlet Microlab fluid handling robots showed up. Its kind of a light duty gantry robot that can do repetitive tasks. A company that builds electron microscopes and FIB machines had bought these to try and automate loading wafers into a SEM. Didnt work out. So they are basically brand new. Here is a video of one:
He had it for a couple months and there was zero interest in it. The software is proprietary and you have to go to them to take a class before they will even sell you the software. Even the company that made it would only offer a pittance for it. The other day it hit me that it would be perfect for a laser cutter. Its completely servo driven. Maxon motors throughout. Rexroth slides on the Y and Z axis and THK on the X. Travel in X and Y is a little more than 36" x24"
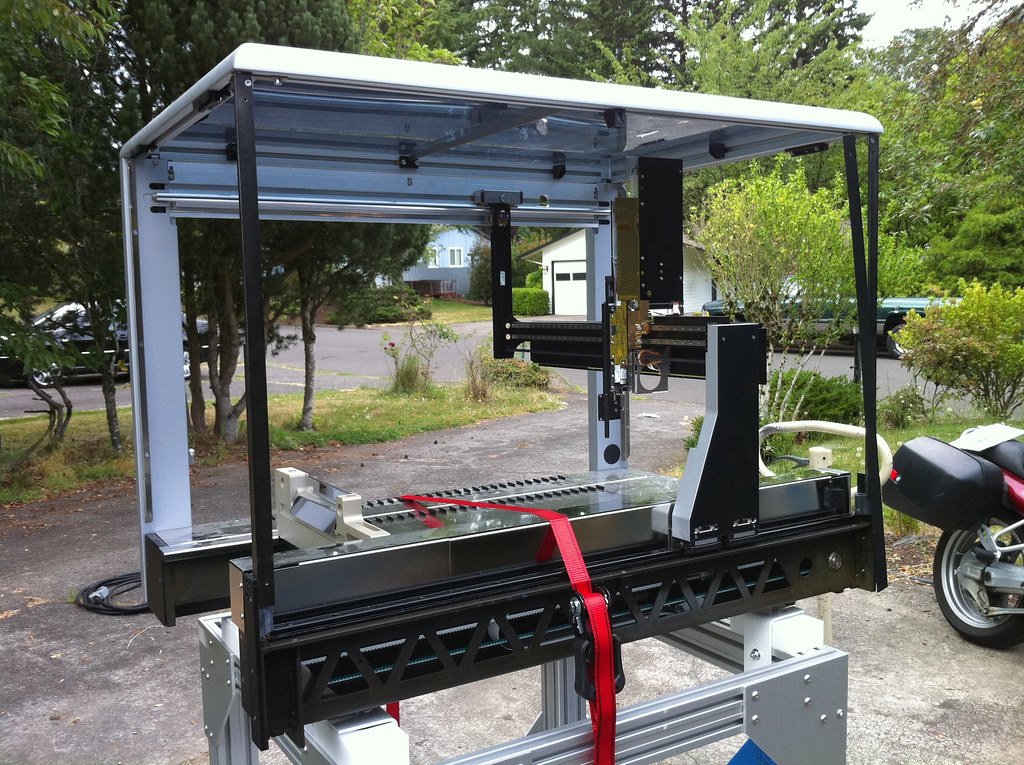
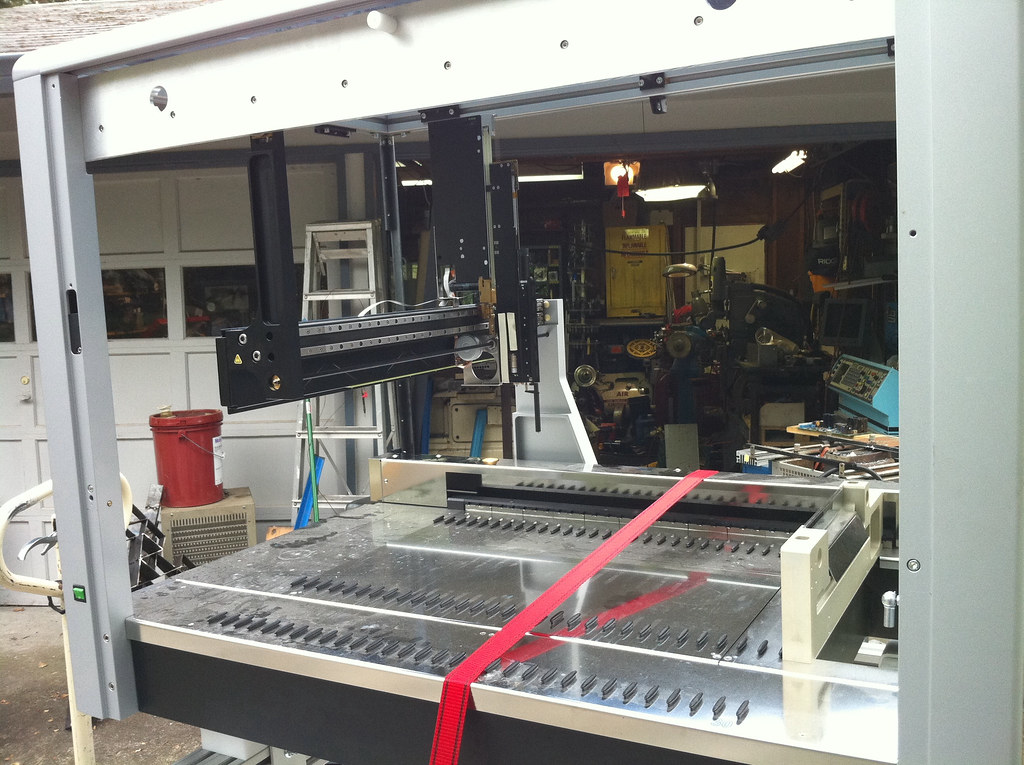
Pic of the main board. Uses dual Infineon processors. Nice 41v, 15A Astec power supply.
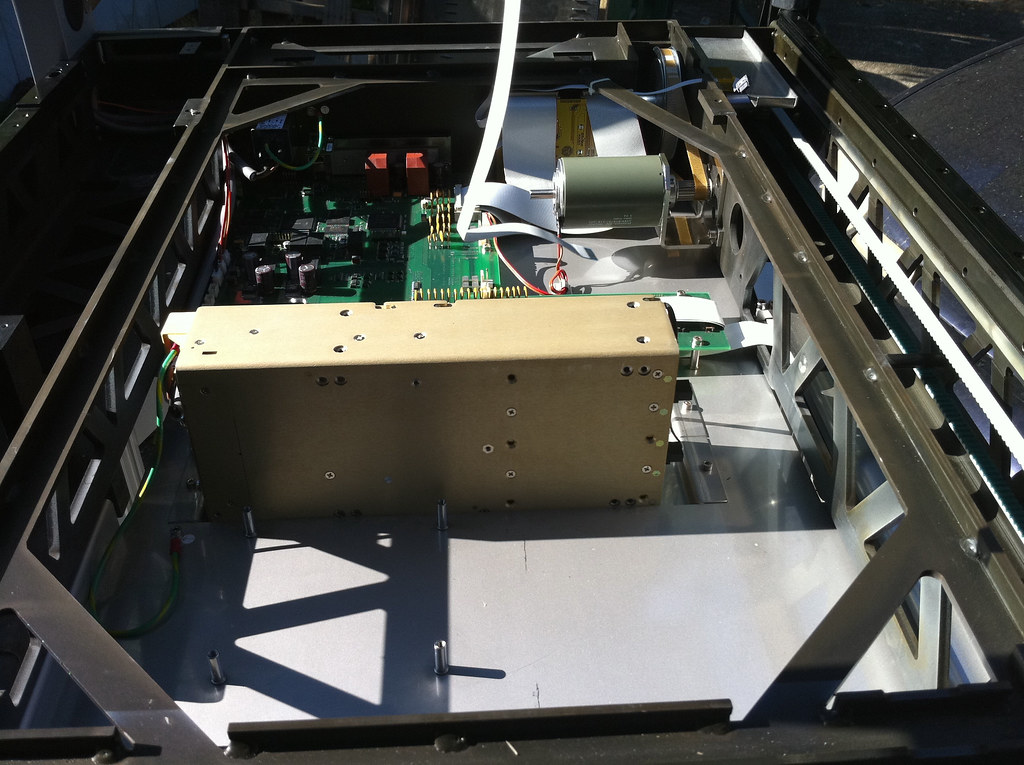
The encoder for the X axis, magnetic, .01mm resolution.

The Y and Z axis. The Y uses a little pancake style brushless motor from Maxon. 30W, 40v or so. It is coupled to a spinning nut that drives it along the leadscrew. The lead screw looks to be 7 starts, 1/2" per turn, 1/4" teflon coated.
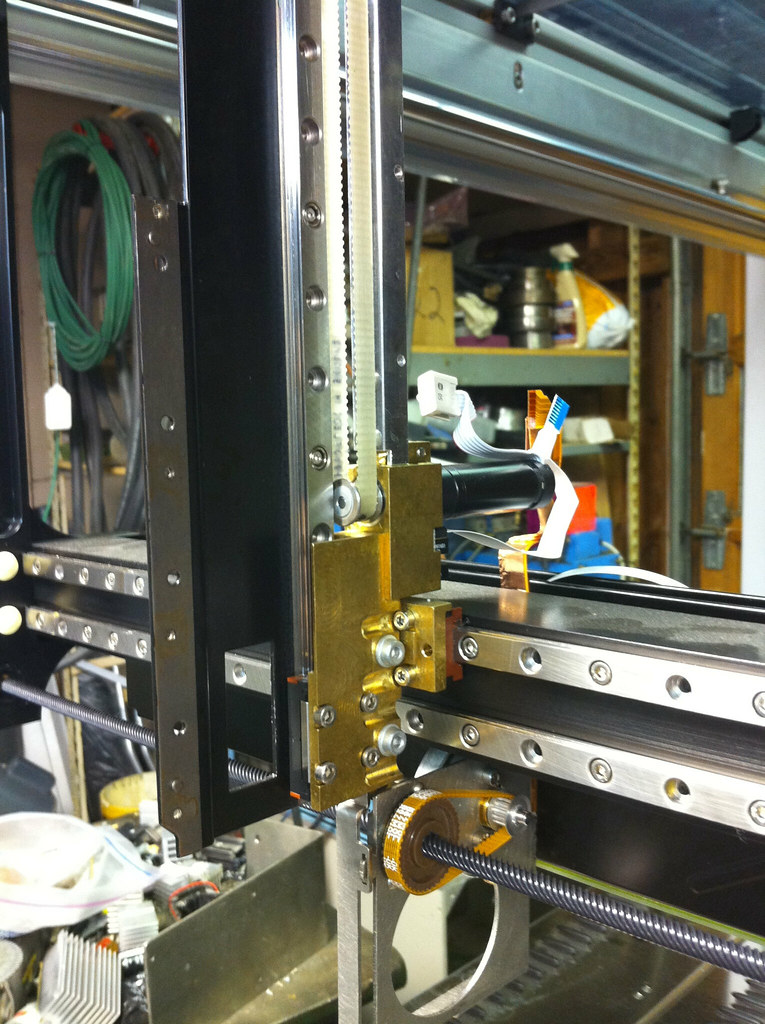
I got a couple servo drives off ebay. They are made by Elmo. Pretty neat little drive, they will run either brushed or brushless motors and you can control them with step and direction pulse inputs in positioning mode. They also have dual loop support so you can have a encoder on the motor and a linear encoder on the axis.