On my RGA system there are two valves the select between wide open and the orifice for high pressure sampling. They are both air operated so I needed something to operate them. I bought one of the 2HP (Yeah, right) little compressors from Harbor Freight years ago. Noisy darn thing. I needed something quieter!
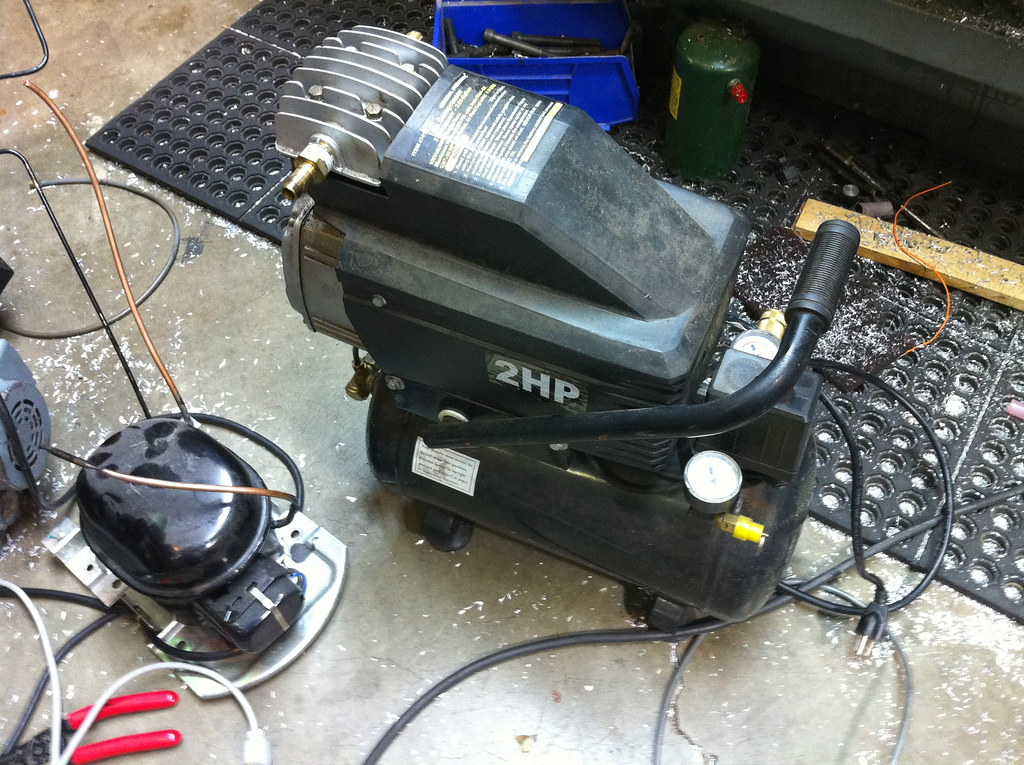
A friend of mine has one of the little Jun-air compressors. They are basically a refrigeration compressor on a tank. The only real difference is the compressor is meant to be able to be worked on. So I figured I would do something similar. I yanked a small hermetic compressor out of a water cooler and welded its mounting bracket to the existing bracket on the compressor tank. Silver soldered on a fitting on the end of the output line and adapted it to the existing line. The only real problem I found is the compressor does not have enough volume to close the unloader valve on the pressure switch. I installed a N.O. 120v solenoid valve in parallel with the motor and connected to the existing unloader line. That has seem to have done the trick. Set the pressure to kick out at 100 PSI. Has no problem getting up there. And most importantly is very quiet!
But it is really slow! I may yet stick a larger pump on there. We'll see. Not like I need it for much. I have a very nice Powerex oilless scroll compressor in the shop.
Yes, I know about lubrication on these pumps. If it goes bad Ill grab another from the scrap yard.
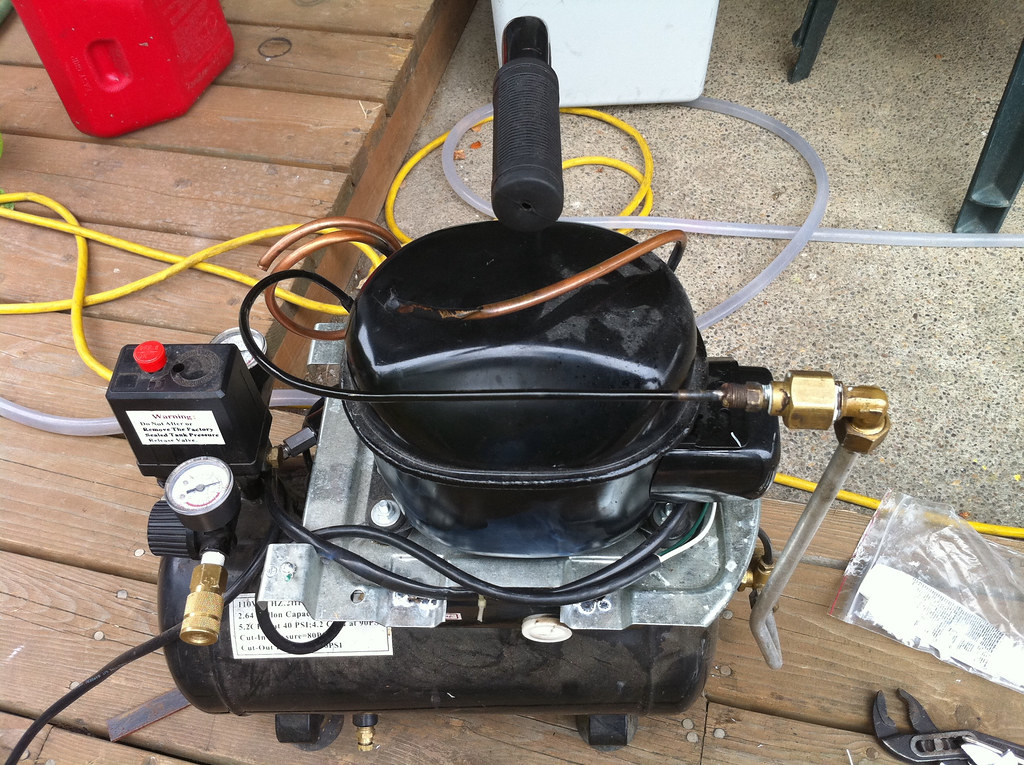